Energy efficiency measurements of machine work in the footsteps of the carbon footprint
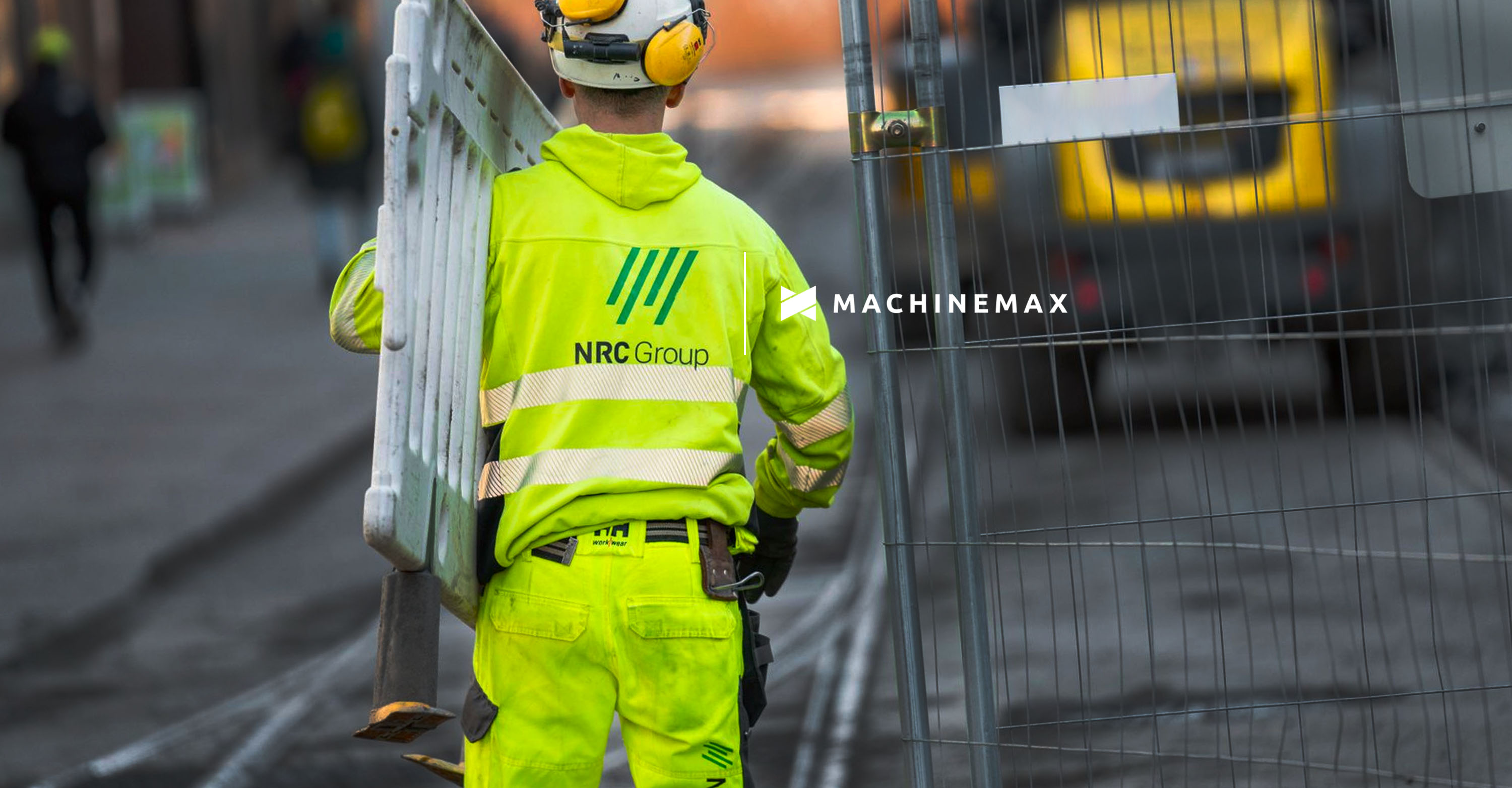
About 85 percent of our direct CO2 emissions come from machine work. In the MachineMax pilot, we studied the energy consumption of our machines and looked for opportunities to reduce machine idling.
We constantly monitor our consumption of electricity, district heating and fuels as part of measuring our carbon footprint. In 2020, NRC Group's Finnish country company had a carbon footprint of 4,101 tonnes, which corresponds to, for example, 839 round-trip flights to Bangkok or 1.2 million Hesburger burgers.
Infrastructure construction and maintenance related to railway tracks is largely mechanical work, and most or about 85 percent of the carbon footprint is generated by the energy consumed by the machines. NRC Group has taken steps towards reducing our carbon footprint.
At the beginning of the year, we set an emission reduction target of 10 percent annually and 30 percent by the end of 2024. To achieve this goal, we need to identify exactly where our emissions come from, says Jukka Viitanen, NRC Group's Environmental Manager.
MachineMax: Towards more energy efficient machine work
According to a study commissioned by Caterpillar, the world's largest machine manufacturer, an average of one third of machine’s operating hours are idle time. The NRC Group wanted to find out, through a pilot with MachineMax, whether their own machines had the same idle percentage.
In the summer of 2021, we piloted the automatic monitoring of our support machinery’s utilization with the intention of getting a detailed understanding of how efficiently they operate, Viitanen says.
In the pilot, the machines were fitted with sensors that measured the vibrations caused by the engine from the machine body. Based on the sensor measurement results, the MachineMax algorithm draws conclusions as to whether the machine is in active work, idling, stationary, or moving from one location to another. In addition, the sensor can be used to determine how many operating hours the machine has per day.
Until now, we have monitored machine work by manually recording various things in our own system during the working day. Automatic measurement reduces the possibility of errors. We have not done the same before, and employees are interested in what the data is highlighting.
A new approach to reducing emissions
The results of the MachineMax pilot in terms of the energy efficiency of the machines will be seen in more detail during the autumn. Part of the idling is, of course, necessary because, especially on the railway track side, the machines must be on standby due to tight working intervals. The aim is to find opportunities in which idling can be reduced and thereby affect the carbon footprint.
The construction sector accounts for 40% of society's total CO2 emissions, but the share of infrastructure construction is not very large compared to, for example, building construction. Perhaps that is why the infrastructure side has not paid as much attention to what could be done to lighten its carbon footprint.
The discussion has focused mainly on switching to renewable fuels or upgrading the fleet to more electric ones. However, from the point of view of life-cycle efficiency and thus also the fight against climate change, it would be better if the existing machinery were better utilized by promoting the efficiency of machinery. That is why before making new investments in machinery or switching to more expensive renewable fuel, it is worth investigating the existing machinery and examining what can be done to reduce the carbon footprint, Viitanen says.